We had an interesting thing happen a couple of years ago: a major Tier 1 Automotive Supplier (we’ll refer to them as T1) contacted us because their customer, a top-selling luxury car manufacturer, was raising the specifications on their paint finish, and T1 was being asked to match.
T1 told us that they could meet the new specifications, but not consistently. They were hoping we could change that. Fortunately, we had a champion at the T1 plant that was familiar with us and with work we had done in other finishing operations.
The Industry is Changing
Most of us in the industry know the importance of automotive paint finish. It doesn’t just protect the vehicle’s surface; it’s the first thing a potential customer sees. It’s also often what forms their overall impression of a vehicle.
Aside from obvious imperfections like runs, blisters, or solvent pops, subtle imperfections like variations in the orange peel texture often have a significant impact on first impression. Auto manufacturers know this and work continuously to improve their finish. As they improve, new expectations are passed to the supplier base.
When we visited T1, we saw a very well-run paint operation. The equipment, the processes, the personnel, and the management were what you would expect from a supplier to a car company with high standards. After the initial meeting, our goal was clear: to determine if our equipment could add exceptional consistency to an already high-performing paint operation.
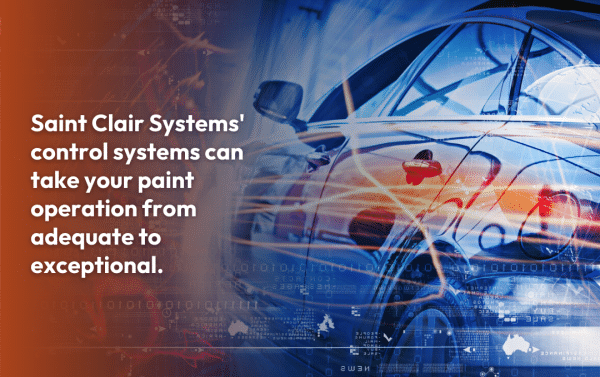
Demonstration
The clearcoat process we were working to improve included parts for both the left side and the right side of a vehicle. We were tasked with working on the right side parts as a direct comparison with the left side parts. The right side would have our temperature control equipment and the left side would continue to run as it had been.
After a short period of time, T1 began to see differences in the orange peel texture. The side with our temperature control was capable of holding a more consistent texture for an entire shift. The left side (no temperature control) was still very good, but it was apparent that there was more variation. Visual comparison supported by results from a BYK-Gardner wave-scan device supported what we expected: the SPC (Statistical Process Control) charts showed a narrowing of the Upper and Lower Control Limits. (For those not familiar with SPC, this is a good thing.)
More Benefit Than Expected
There was also one unexpected benefit: T1 was using measurably less clearcoat on the side with temperature control and achieving better results. During one shift, they used approximately 10% less clearcoat material with temperature control. By stabilizing the temperature, we were able to stabilize the flow out of the clearcoat and manage the rate at which solvent evaporated from the coating. This combination allowed us to improve quality while using less material.
If you’re wondering if we can achieve similar results in your operation, contact us. We can schedule a demonstration and find out.
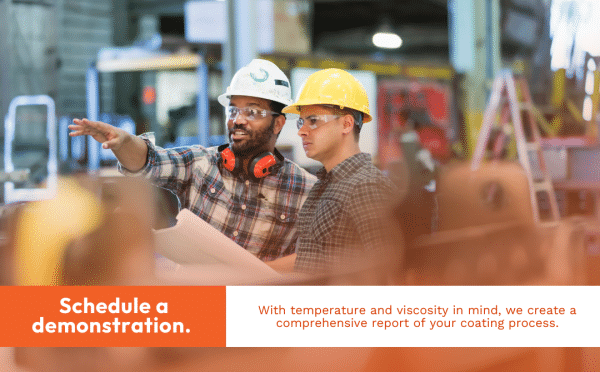